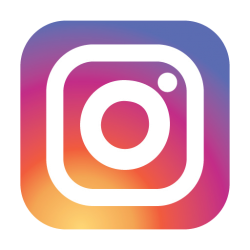

Ha napjaink technológiai forradalmáról beszélünk, leggyakrabban az ipar 4.0, a digitalizáció, a robotika, vagy a mesterséges intelligencia jut eszünkbe, holott a technika fejlődése egyre gyakrabban illeszti be ebbe a sorba a 3D nyomtatást, azaz az additív gyártást is. A módszer alapjaiban változtatja meg a gyártástechnológiával kapcsolatos korábbi tudásunkat. A klasszikus öntés és a forgácsolás mellett ugyanis megjelent a tárgyakat rétegről rétegre, a legváltozatosabb formában és szerkezettel felépíteni képes additív technológia. A Szegedi Tudományegyetemen 2021-ben nyitották meg a 3D Központot, melynek szakmai vezetője, dr. Geretovszky Zsolt adott interjút a Kamarai Futár szaklapnak erről, a hazánkban még úttörőnek számító technológiáról.
– Ön előadásain additív forradalomnak szokta nevezi azt a folyamatot, ami az elmúlt 40 év során a 3D nyomtatás területén bekövetkezett. Mi történt?
– A ma additív gyártásnak hívott technológiával kapcsolatos első ötletek az 1980-as évek elején jelentek meg Japánban és Franciaországban, akkor még, mint a gyors prototípus-készítés egyik lehetséges eljárásaként. Azonban aki először látott üzleti fantáziát a rétegről rétegre építkező módszerben, az egy amerikai kutató, Chuck Hull volt. Sztereolitográfiaként ismert módszerének szabadalmaztatása után 1986-ban megalapította a 3D Systems vállalatot, ami máig működik és meghatározó szereplője az additív területnek. Ők dobták piacra az első, kereskedelmi forgalomban is kapható 3D nyomtatót, az SLA-1-et. Az ezt követő tíz évben aztán gombamód jelentek meg azok a technológiák, amelyek ezt a rétegről rétegre történő építkezést meg tudják valósítani. És közben újabb és újabb alkalmazási ötletek születtek. Rájöttek ugyanis, hogy az additív elven alapuló mintakészítés egyik különleges tulajdonsága, hogy az alakzat formáját, geometriáját jóval szabadabban, sokkal kevesebb korláttal választhatják meg. És ez nagyon sok területen megmozgatta az emberek fantáziáját. Így ma már az élet szinte minden területén találkozhatunk 3D-ben nyomtatott tárgyakkal, a fülbevalóktól az épületekig. És ha már méretek. A hajszálunk vastagságától a szegedi dóm magasságáig (81 méter) a legkülönbözőbb méretekben tudunk nyomtatni 3D-ben.
– Miben más ez a technológia, és mit értünk pontosan a tárgyak additív előállításán?
– A klasszikus gyártástechnológiáknak két alaptípusa van, az egyik, amikor a formába öntjük az adott testet, ilyen például a fröccsöntés, a másik, amikor egy nagyobb, „nyers” darabból pl. forgácsolással, marással választjuk le a felesleges anyagot és a megmaradó rész lesz a késztermék. Talán nem kell bizonygatni, hogy a folyamat mekkora anyagveszteséggel jár. Ezen megoldásokkal szakított gyökeresen az 3D nyomtatás, amely alulról, azaz építőelemeiből „kirakott” vékony rétegekből építi fel a testet. Ezt hívjuk ma additív gyártásnak, közismertebb nevén 3D nyomtatásnak. A folyamat hasonlít ahhoz, amikor a kőműves a tervrajz alapján rakja a téglákat, sorról sorra, egyforma rétegekkel halad felfelé, míg el nem éri az épület első szintjének magasságát, majd tervrajzot vált és a következő szinten folytatja munkáját. A 3D-s nyomtatás egy lényeges dologban különbözik a ”házépítés” példájától: a 3D nyomtatott test akár minden egyes téglasora, azaz rétege különböző tervrajz alapján készülhet, s ezáltal változatosabb alakzatok létrehozására vagyunk képesek.
Forrás: Kamarai Futár
– Hogyan képzeljük el egy 3D nyomtató működését? Hogyan és miből képesek a különféle rétegeket előállítani és szabályos testté építeni?
– Az additív gyártásnak jelenleg hét különböző fajtáját ismerjük, amelyek csak annyiban különböznek, hogy a lerakott anyagot hogyan szilárdítják meg. A porágyas alaptechnológia lényege, hogy egy lefókuszált lézer- vagy elektronnyaláb olvasztja össze egy leheletvékony porréteg porszemcséit, amelyet korábban egy porterítő mechanika terített le – a fémnyomtatók többnyire ezen az elven működnek. Az első, szabadalmaztatott 3D-s megoldásnál, az ún. kádas fotopolimerizációnál egy viszkózus műgyanta közeget szilárdítunk meg, legtöbbször ultraibolya fény segítségével. Az irányított energiával történő 3D nyomtatásnál szintén fémport és lézert használnak, csak itt a por lerakása és megolvasztása egyidejűleg történik: a vivőgáz által szállított fémport egy, a gázjetet keresztező lézernyaláb „röptében” olvasztja a nyomtatott test épp épülő pontjára. A folyadéksugaras technológia a tintasugaras nyomtatókhoz hasonló elven működik: az ilyen nyomtatókban az elektronika akár több ezer fúvóka vezérlésével nagyon pici folyadékcseppekből álló műgyantafüggönyt hoz létre, és az ezen cseppekből megszilárduló anyag alkotja a test építőköveit. Ismerjük a kötőanyag-porlasztásos technológiát is, ami a folyadéksugaras és porágyas technológiák kombinálása, amelynél a por formában kiterített építőanyagot apró kötőanyagcseppek segítségével ragasztják össze. Végezetül a hetedik technológiai család, amelyet extrudálásos módszernek hívnak, legismertebb változata a szálolvasztásos nyomtatás, amikor egy hőre lágyuló műanyagszál biztosítja az építőanyagot. Ennél a melegítéssel meglágyított anyagot egy kis átmérőjű fúvókán préseljük ki, ami visszahűlve megszilárdul – hasonlóan ahhoz, ahogy a technikaórán, vagy barkácsolás során a ragasztópisztollyal dolgozunk. Ez egyébként az egyik első, és máig a legolcsóbb 3D nyomtatási technológia. Ha valaki szeretne otthonra ilyen, szálolvasztásos 3D nyomtatót, már néhány százezer forintért vállalható minőségű eszközt vehet magának.
– Laikus szemmel ezeknek a technológiáknak a kitalálása volt a nagy truváj, a működtetése talán már nem annyira…
– Bár látszólag a nyomtatók egyszerűen működnek, de egyrészt igen komoly műszaki kihívás stabilan tartani a nyomtatási folyamatot akár több tíz órán keresztül úgy, hogy azzal hajszálnál vékonyabb rétegeket építünk egymásra. Másrészről maga a nyomtatás csak egy lépés a „gyártás” viszonylag hosszú láncolatában. A teljes technológia ugyanis viszonylag sok előkészítést igényel: számítógépen meg kell terveznünk a testet 3D-ben, utána el kell azt helyeznünk, és orientálnunk kell a nyomtatási térben, szeleteléssel létre kell hoznunk azokat a file-okat, amelyeket a gép a nyomtatásnál a rajzolatok létrehozásához használni fog. Komolyabb, ipari igényekre nyomtatott tárgyak esetén ma már le is kell szimulálnunk a nyomtatást, és csak ezt követően jöhet a tényleges nyomtatás. Ráadásul a nyomtatási job végeztével sem vagyunk még kész, mert a gyártás befejező fázisában sor kell, hogy kerüljön utómunkálatok elvégzésére is, aminek – ipari alkalmazás esetén – a minőség-ellenőrzés is része, hogy megtudjuk, azt kaptuk-e, amit szerettünk volna.
– Mit lehet nyomtatni a 3D nyomtatóval és miből?
– Ma már elég sokfajta anyagot, fémeket, ötvözeteket, többféle műanyagot, nemcsak hőre lágyulót, hanem hőre keményedő műgyantát is, kerámiákat, de a gasztronómiában különféle élelmiszereket is nyomtatnak. Mivel sokkal nagyobb szabadsággal tudunk létrehozni geometriákat, mint bármi más klasszikus technológiával, ezért megtehetjük, hogy a tárgynak a funkcióját helyezzük előtérbe, nem pedig azt, hogy létre tudjuk-e azt hozni. Vegyünk példának egy széket – a klasszikus technológiáknál fontos szempont, hogy olyan elemekből, alkatrészekből készüljön, amelyeket elő tudnak állítani, és az elemekből össze is tudnak szerelni. Ezzel szemben, ha 3D nyomtatással készítünk egy széket, ezekre nem kell figyelnünk. Számos geometriai kényszer kiesik, azt mondjuk a tervezőnek, álmodhatsz bármit, és „csak” pár logikus funkcionális elvárást támasztunk: legyen egy kb. 80 cm magasan kialakított ülőfelülete, bírjon el pl. 150 kilót, álljon stabilan és igény szerint legyen háttámlája. Nagy rá az esély, hogy egy ilyen feltételek mentén, de geometriai kötöttségek nélkül, ún. generatív módon tervezett szék klasszikus eljárásokkal nem, de additív módon létrehozható lesz.
– A részek tömbösítésével változnak-e a kinyomott darabok mechanikai tulajdonságai?
– A geometriai szabadsággal nemcsak könnyebb, hanem erősebb is lehet a 3D nyomtatatott termék az eredetinél (lásd keretes írásunkat – a szerk.). Ugyancsak fontos szempont lehet, hogy sok esetben olyan alkatrészeket, amiket korábban több darabból állítottak össze, kinyomtatni akár egyben is ki lehet. A GE első ilyen, addítív technológiával gyártott terméke egy repülőgép- hajtómű fúvókarendszere volt, ahol kb. 180 alkatrészt váltottak ki egyetlen nyomtatott alkatrésszel úgy, hogy közben még könnyebb és gazdaságosabb is lett a termék, és ezért az ilyen fúvókával szerelt repülők kevesebb károsanyag-kibocsátással tudnak repülni. De ma már pl. egyes Bugattik fémblokkját is egyben nyomtatják ki.
Az igazi durranás nem feltétlen az, hogy mondjuk, egy tíz alkatrészből álló egységet egyben kinyomtatunk, hanem az, ha a funkciójának megfelelően olyan darabot tudunk előállítani, amely jobb is lesz, tulajdonságaiban többet tud, mint az eredeti, több részből összerakott egység. Ha egy alkatrésznek pl. vannak tömör részei, additív módon előállítva, ezeknek egyáltalán nem kell tömörnek lenniük. És bármilyen meglepő is, de egy kevesebb anyagból álló ilyen rácsszerkezet erősebb és szilárdabb is lehet, mint a tömör megfelelője.
Forrás: Kamarai Futár
– Minden életképes vállalkozás folyamatos fejlesztésben, innovációban, a versenyképesség növelésében gondolkodik – kiknek érdemes megismerni és belevágni egy 3D-s fejlesztésbe?
– Tíz évvel ezelőtt a különféle felmérésekben a megkérdezett cégek döntő része erre a kérdésre azt válaszolta, azért lát fantáziát a 3D nyomtatásban, mert azt prototípus készítésére akarja használni. Ma már a többség azt válaszolja, valamit elő szeretne vele állítani, vagyis nem csak egyszeri alkalomra, hanem valaminek a gyártására szeretné használni a 3D nyomtatást, mégpedig olyan alkatrészére, ami a hagyományos gyártástechnológiákkal elérhetetlennek gondolt előnyöket is hordoz. Ma már a piacon elérhetőek olyan 3D nyomtatók, amelyeket kimondottan úgy fejlesztenek, hogy azokat gyártósorba lehessen integrálni. Ehhez persze magas fokú szaktudásra van szükség. Ugyanezen felmérésekből az is kiderült, hogy a megkérdezett cégvezetők szerint az additív technológia elterjedésének jelenleg legnagyobb gátja az, hogy hiányzik az a szürkeállomány, amely képes a technológia nyújtotta lehetőségek kiaknázására. A technológiai specifikumok ismerete tehát komoly piaci előnyt jelent minden 3D technológiát alkalmazó cégnek. Mi ebben is próbálunk segíteni.
– Ha egy vállalkozás komolyan érdeklődik a 3D nyomtatás iránt, hol kezdje?
– Szívem szerint azt mondom, hogy jöjjön be hozzánk. Nyilván sok minden megtalálható az interneten is, de mindenképpen olyan helyen kérjen tanácsot, ahol széles spektrummal, nagy rálátással ismerik az additív területet. A SZTE IKIKK 3D Központja ilyen hely, legalább a régióban, de tudtommal országosan is. És engedjen meg még egy idevágó gondolatot. Ahhoz, hogy valaki komolyan kezdjen foglalkozni a 3D nyomtatással, még egy feltétel elengedhetetlen: a nyitottság. Nyitottság arra, hogy lehet valamit a korábbi ismereteitől, meggyőződésétől eltérő módon másképp, más alakban, akár más anyagból, máshogyan is elkészíteni. Persze úgy, hogy a 3D nyomtatott termék a célra, feladatra tökéletesen meg fog felelni.
– Mit tud ebben segíteni a szegedi 3D Központ?
– Központunk küldetése az oktatás és a kutatás támogatása mellett a szolgáltatás is – az akadémiai és az egyetemen kívüli közösségek számára egyaránt. Eszközparkunk és mindaz, amit mi szürkeállományban tudunk, az önök, az érdeklődők rendelkezésére áll. Az egész régiónak kínálunk lehetőséget, egy olyan kompetenciaközpontot, ahová el lehet jönni – tájékozódni, konzultálni, kipróbálni. Ha valakinek van egy ötlete, amire saját rutinjából azt gondolja, hogy úgysem megvalósítható, mi azt is szívesen meghallgatjuk. Eddig még több olyan példánk van, amikor találtunk megoldást a kihívásra, mint amikor nem. Ha valaki azt kéri, hogy tervezzünk meg egy 3D objektumot; szkenneljünk be valamit, és nézzük meg, hogyan néz ki nyomtatva; vagy nyomtassunk ki egy file-t, megcsináljuk. A Központban egyébként több szálolvasztásos és műgyantás nyomtatónk, valamint porágyalapú fémnyomtatónk is van. Ez utóbbinál a kinyomtatott fémtárgyakat feszültségmentesítő hőkezelésnek is alá kell vetni, amihez van megfelelő kemencénk is. Ezt is igénybe veheti bárki, akkor is, ha nem nálunk nyomtatta ki a hőkezelendő objektumot. Hisszük, hogy az SZTE 3D Központja az a hely, ahol az additív gyártás tanulható, művelhető, fejleszthető és alkalmazható.
– A 3D technológia komoly hódító utat jár be az élettudományok területén is, és akkor már közeledünk az SZTE 3D Központjának egy fontos profiljához.
– A tudomány és orvoslás mindenképpen olyan területek, ahol mindig van igény az újszerű megoldásokra. Gondoljunk csak bele, amikor valakinek komoly sebészeti beavatkozásra van szüksége, és az implantátumot, amivel például egy törött csontot pótolnak, néhány standard méretből kell kiválasztania az orvosnak – gyakran kénytelen a beteget „faragni” az implantátum helyett. Ma már a 3D nyomtatás teljesen egyedi implantátumok készítését is lehetővé teszi. Sok embernek van szüksége végtagpótlásra, illetve ortézisekre is, ezek közül az egyik, széles körben elterjedt 3D nyomtatott termék a hallókészülékek köre, nagyrészt azért, mert hallócsatornáink egyedi formájúak. Végtagpótlásnál pedig az is fontos szempont lehet, hogy a funkcionalitás megtartása mellett az egyedi esztétikai igényeket is figyelembe lehessen venni. A 3D nyomtatott művégtagok ezen a téren is jelentősen szélesítik az elérhető és megfizethető lehetőségek tárházát.
Könnyű belátni, hogy számos orvosi beavatkozás hatékonyabban, gyorsabban, eredményesebben, rövidebb idő alatt, kevesebb fertőzésveszéllyel végezhető, ha az orvoscsoport be tudja gyakorolni a műtétet. Laboratóriumban már demonstrálták, hogy akár szívet is ki lehet nyomtatni, és pár éve egy komplett 3D nyomtatott alsó állkapcsot implantáltak egy holland betegbe. Ezek az orvosi modellek nagyban hozzájárulnak a műtéti beavatkozás sikerességének javításához. Gondoljunk csak az arcsebészeti műtétekre, amikor az orvos megpróbálja összerakni a beteg arcát úgy, hogy hasonló legyen ahhoz, amilyen a baleset előtt volt. Az egyszerhasználatos műtéti segédeszközök előállításában is egyre gyakoribb módszer az additív gyártás. Fontos szerepe formálódik az additív technológiának az orvosképzésben is, hiszen 3D nyomtatás segítségével komplex és kézbe vehető vizualizációt tudunk biztosítani az emberi testről, akár annak bármely porcikájáról. Mi pl. a legkisebb szervünk, a hallószerv nyomtatásával is foglalkozunk, beleértve ebbe az emberi test legkisebb csontjainak, a hallócsontocskáknak a nyomtatását is.
– A fejlődés tempóját lehet-e valahogy érzékeltetni?
– Egy olasz cég csípőimplantátumok 3D nyomtatással történő előállításával 2020-ban jelent meg a piacon, amelynek a legkritikusabb része a csípőcsontba illeszkedő combcsontimplantátum. A 3D nyomtatott implantátumról bebizonyosodott, gyorsítja a csontosodást, a beteg mielőbbi felépülését. Ugyanez a cég 2021-ben megnyitotta az első kihelyezett, kórházi környezetben működő komplex Ortopédia Központját New Yorkban. Az orvosok a CT-képet leküldik a központnak, ott megtervezik az egyedi implantátumot, a kinyomtatott terméket megkapják az orvosok, és sterilizálás után – jellemzően egy nap múlva – már ültethetik is be azt a betegbe. A fejlődés ütemét jól mutatja, hogy az elmúlt bő 2 évben közel száz hasonló centrum nyílt világszerte. Éves szinten egyébként 15-20 százalékkal növekedik az additív gyártású ortopédiai eszközök piaca.
– Mit ad hozzá Szeged az additív technológia fejlődéséhez, és jellemzően milyen kutatási irányok művelői adják fel a leckét a 3D Központ szakembereinek?
– Az SZTE IKIKK 3D Központja azzal a küldetéssel jött létre, hogy inspiráló szakmai környezetet és kurrens infrastruktúrát biztosítson a Szegedi Tudományegyetemen az additív gyártás és a hozzá kapcsolódó digitális 3D technológiák területeinek műveléséhez és az azokban rejlő potenciálok minél teljesebb körű kiaknázásához. Az egyik vegyész csoport például azzal foglalkozik, hogy folyadékokból nagyon kis mennyiségű anyagmeghatározást, nyomelem-analitikai és nanorészecske-mérési feladatokat tudjanak elvégezni. Mi egy 70 mikron sugarú csövet, ún. kapillárist tartalmazó porlasztót nyomtattunk a kísérleteikhez (ez kb. olyan átmérőjű, hogy egy hajszállal tele lenne). Az Anatómiai, Szövet- és Fejlődéstani Intézet egyik csoportja pedig azzal kereste meg a Központot, hogy szeretnék az idegsejteket egyirányú növekedésre bírni. Ehhez olyan, kb. 100 mikron széles és 40 mikron mély csatornákból álló rendszert sikerült számukra létrehoznunk, amiben az idegsejtek már szépen és irányítottan növekednek. Egy másik projektünk a Gyógyszerésztudományi Karhoz kötődik, akikkel közösen egy vékony, kb. egy milliméter hosszú tűkből álló „fakírszőnyeget” nyomtatunk, amivel, ha megszúrják a bőrt, az nem fáj, hiszen ezek a mikrotűk nem érik el a bőrben levő idegvégződéseket. A mikrotű mátrix segítségével ugyanakkor a bőrbe ott és nagyobb lokális koncentrációban tudják bevinni a hatóanyagot, ahol arra szükség van.
A műtéti támogatásoknak is széles a köre, az Orvosi Fizikai és Orvosi Informatikai Intézet fejlesztéseihez például légcső-, a rektor úr klinikai csoportjának pedig belsőfül modelleket nyomtattunk – az ilyen munkákkal a műtéti tervezéshez, gyakorláshoz és betegtájékoztatáshoz egyaránt támogatást tudunk nyújtani.
Akkreditált 3D képzés ugyan még nincs az egyetemen, de már itt van ez a Központ, ahol meg lehet tapasztalni a technológia előnyeit, korlátait, vannak kurzusaink, de a hallgatók a különféle kutatómunkákba bekapcsolódva is egyre gyakrabban kerülnek kapcsolatba a 3D nyomtatással.
Névjegy
Dr. Geretovszky Zsolt Szegeden doktorált, majd éveket töltött a londoni UCL-en, illetve a svédországi Lund egyetemén. 2016 óta habilitált docensként vezeti a Természettudományi és Informatikai Kar Fizikai Intézetének Nano- és Mikromegmunkálási Laboratóriumát. Szakterülete a lézeres anyagmegmunkálás, nanorészecskék fizikai úton történő előállítása, valamint az additív gyártás és ezek alkalmazási területeinek kutatása. Kezdeményezésére jött létre az SZTE IKIKK 3D Központja, amelynek 2022 óta szakmai vezetője.
Forrás: Kamarai Futár
Metaanyogokkal kísérleteznek
Mint dr. Geretovszky Zsolttól megtudtuk, az utóbbi évek egyik kutatási területe az úgynevezett metaanyagok előállítása. Ahogy a központ vezetője elmagyarázta, ez azt jelenti, hogy olyan elemi cellákat hoznak létre, amelyek szabad szemmel már láthatók, és ezekből építenek fel egy viszonylag „szellős” szerkezetet, amit úgy lehet elképzelni, mint egy speciális állványzatot. Ezen belső szerkezettel rendelkező metaanyagokkal előnyösebb mechanikai tulajdonságokat – például szilárdság, teherbíró-képesség – tudnak létrehozni, mintha tömör anyagból dolgoznának. Tavaly óta Szegeden is nyomtatnak ilyen mintákat – amelyeken a mintázatok sűrűségét variálták. És bizony erősebbnek bizonyulnak azok a minták, amelyek kevesebb anyagot tartalmaznak, tehát egyszerre könnyebbek és mechanikailag ellenállóbbak, mint tömör megfelelőik. „Az az izgalmas ebben – mondta a tanár úr –, hogy a természet sokszor hasonló szerkezeteket fejlesztett ki bennünk, például a csontjainkban. Ha tömör lenne, mondjuk a combcsontunk, sokkal törékenyebb lenne, azzal az inhomogén (térben változó) szivacsos szerkezettel, amelyet a metaanyagokkal mi is le tudunk másolni.”
Ma egyébként már nyomtatnak csontot is, 3D – bionyomtatással. Ehhez olyan, ún. őssejteket használnak a nyomtatás során, amelyek képesek, még a funkciójuknak megfelelően differenciálódni.
Forrás: Kamarai Futár
Készítette: Őrfi Ferenc
Forrás: Kamarai Futár. A Csongrád-Csanád Megyei Kereskedelmi és Iparkamara lapja
www.csmkik.hu